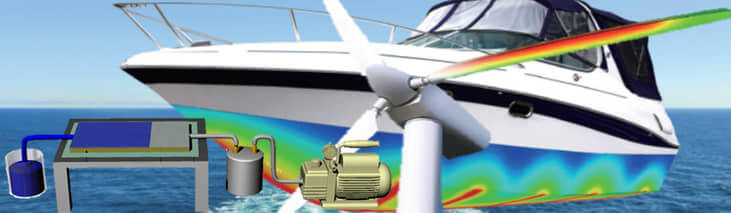
Resin Transfer Moulding (RTM) or vacuum fusion is manufacturing process extensively used by manufacturers in the aerospace, maritime, automotive and energy sectors. The technique can generally be described as the process where an epoxy or thermoset resin is infused with a reinforcement or fibre material. Resin is sucked with the help of a vacuum pump through the part, consisting of fibre materials and/or core material. A vacuum trap is incorporated in the vacuum line to prevent the liquid resin from damaging the vacuum pump or pipe network. The product has very favourable strength-to-weight, stiffness and corrosion-resistant characteristics and can accommodate shapes for parts that conventional manufacturing does not allow.

The moulding process, however, does come with its challenges. One of the biggest headaches is to minimize resin-to-material ratio, ensuring that only enough resin is used to form the part’s structural integrity while avoiding short fills or dry reinforcing material. Overfill will cause the part to contain additional resin material without contributing to its strength, increasing material costs. The process can also produce inconsistent thicknesses through the length and width of the part, not to mention air traps, shrinkages and premature resin curing. There is also no easy way to determine the correct setup for the vent plumbing, decreasing quality certainty and increasing experimental time and costs.
In the backdrop of smarter manufacturing and sustainable development, Moldex3D is assisting manufacturers to meet the ever increasing industry demand for part performance, advanced shape requirements and reduced costs. Moldex3D’s Resin Transfer Moulding (RTM) module assists engineers and manufacturers to accurately predict the resin flow and curing characteristics of composite lay-up part. The Computer Aided Engineering (CAE) simulation software has become popular for the solution it provided for injection moulding application. RTM is an additional CAE tool characterising flow, heat, cure and shrinkage properties of thermosetting and thermoplastic processes.
Utilizing their CFD and nonlinear solver technologies, Moldex3D utilises iso-thermal analysis for different applications and cases. The solution allows the user to validate and visualise flow behaviours, resultant warpages and curing effects of the resin. The user can setup up multiple runs to experiment with different vent layouts, multi inlets, pressure and flow rates, without consuming costly resources like material, equipment and labour. Advanced inlet controls can be modelled to explore alternative resin feeding flows to prevent premature curing and inconsistent thickness anomalies, similar to what is seen in the real world. Dependant on the design, different material layers, orientations and core thicknesses can be explored to determine material permeability. Moldex3D RTM can model different fibre orientations and material properties for each layer of the designed part to investigate the effects thereof.

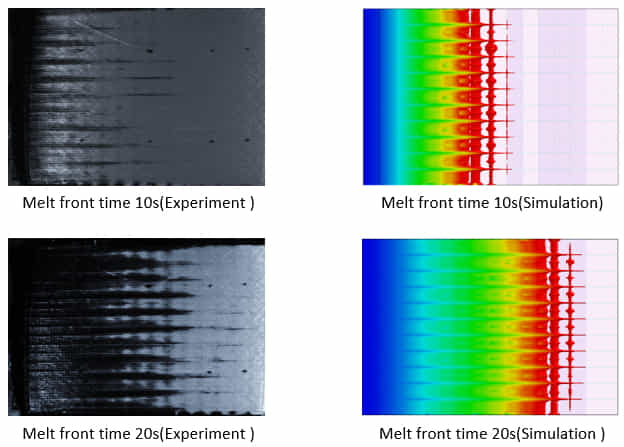
The benefits are hard to ignore for advanced composite material manufacturing processes. Not only are development times decreased for each and every individual part, but resource consumption are reduced in terms of materials, labour and infrastructure. Potential manufacturing flaws can be identified before the time consuming preparation and processes are started. Furthermore, existing error-free process can be revisited to ensure procedures are optimal in terms of curing times and costs.